Exploring the Conveniences of a Chemical Defoamer in Manufacturing and Production
The assimilation of chemical defoamers in production and manufacturing procedures provides a calculated benefit by resolving one of the relentless challenges in commercial operations: foam control. As producers aim to maximize procedures and improve client satisfaction, the function of chemical defoamers comes to be progressively essential.
Relevance of Foam Control
While the existence of foam in producing processes can often seem safe, effective foam control is vital for enhancing functional performance and product high quality. Foam can hinder various stages of manufacturing, bring about inefficiencies that might raise expenses and extend handling times. In sectors such as food and drink, pharmaceuticals, and chemicals, unchecked foam can obstruct tools, interrupt automated systems, and ultimately result in product disparities.

Carrying out reliable foam control strategies not just enhances productivity yet likewise supports regulatory conformity in markets where foam can lead to environmental problems. By using chemical defoamers, producers can alleviate these obstacles, ensuring smoother procedures and higher-quality output. Eventually, focusing on foam control is a crucial element of manufacturing that can yield substantial advantages in terms of safety and security, item, and effectiveness integrity.
Types of Chemical Defoamers
What kinds of chemical defoamers are offered for producing procedures, and exactly how do they vary in application? Chemical defoamers can be categorized into three major types: silicone-based, organic, and inorganic defoamers. - Chemical Defoamer

Organic defoamers, commonly acquired from fatty acids or natural oils, work in a series of applications, consisting of food and beverage production. They are typically preferred for their reduced toxicity and ecological impact, ensuring compliance with industry laws.

Each kind of defoamer offers distinct objectives based upon the chemical composition and the certain demands of the production procedure, allowing makers to pick the most appropriate choice for their specific needs.
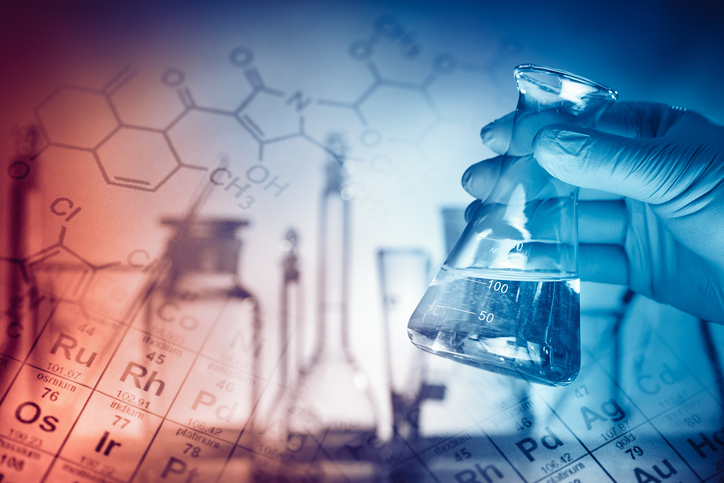
Advantages in Production Efficiency
Chemical defoamers play a vital function in enhancing manufacturing effectiveness by properly controlling foam generation throughout different processes. Foam can prevent production prices, disrupt equipment operation, and bring about costly downtime. By integrating chemical defoamers, producers can mitigate these problems, making sure smoother operations and increased total performance.
Using chemical defoamers helps optimize the functional efficiency of devices such as pumps, mixers, and reactors. With decreased foam, these equipments can operate at their intended capacity, lessening the threat of overflow and enabling regular handling. This causes better resource utilization and greater throughput.
Furthermore, chemical defoamers help with faster processing times by reducing the time needed for foam removal. This acceleration can substantially affect manufacturing timetables, allowing this website makers to meet client need better. Additionally, making use of defoamers adds to decrease power usage, as equipment operates more effectively with lowered foam disturbance.
Effect On Item High Quality
Foam control is not only necessary for maintaining effectiveness in producing processes but likewise plays a considerable duty in ensuring product quality. Too much foam can present air into solutions, bring about inconsistencies in the end product. This can manifest as flaws such as spaces, unequal textures, or substandard coatings, which undermine the intended high quality and performance of the item.
Moreover, foam can hinder the homogeneity of mixes, leading to uneven circulation of active ingredients. In industries such as layers, cosmetics, and food production, this can bring about variants in color, preference, and general efficiency. By utilizing a chemical defoamer, manufacturers can minimize these risks, guaranteeing that products meet stringent quality requirements.
In addition, controlling foam can enhance the stability of emulsions and suspensions, which is crucial for guaranteeing shelf-life and customer satisfaction. With improved product uniformity and lowered problems, suppliers can accomplish greater standards of quality control, ultimately resulting in boosted consumer count on and brand commitment.
Cost-Effectiveness and ROI
Efficient foam control not just enhances product top quality but additionally adds considerably to the general cost-effectiveness of making processes. Making use of chemical defoamers decreases foam-related concerns, which can or else bring about production hold-ups, devices malfunctions, and increased power intake. By reducing foam, manufacturers can maximize their processes, leading to higher throughput and effectiveness.
Buying chemical defoamers can produce a considerable return on financial investment (ROI) The preliminary expenses related to these ingredients are commonly pop over to these guys countered by the cost savings realized from decreased downtime and boosted product return. Boosted item top quality can reduce waste and revamp expenses, even more boosting monetary performance.
Furthermore, efficient foam control can lead to reduced water and power usage, contributing to lower operational costs. This is especially essential in industries where resource effectiveness is paramount. By integrating chemical defoamers right into their procedures, makers can accomplish long-lasting financial savings while preserving competitive rates in the marketplace.
Final Thought
In conclusion, the combination of chemical defoamers in manufacturing and manufacturing procedures is crucial for enhancing functional performance and enhancing item high quality. The benefits provided by chemical defoamers not only sustain governing conformity yet also offer a competitive view publisher site edge in the production landscape.
The combination of chemical defoamers in manufacturing and manufacturing processes provides a calculated advantage by resolving one of the persistent challenges in industrial procedures: foam control.While the presence of foam in making processes can sometimes appear harmless, reliable foam control is essential for enhancing operational performance and product quality.Chemical defoamers play an essential duty in improving making effectiveness by properly controlling foam generation throughout different procedures.In addition, chemical defoamers promote faster processing times by decreasing the time required for foam elimination. Additionally, the usage of defoamers contributes to decrease power intake, as machinery runs much more effectively with minimized foam disturbance.